After eight months of hard work, I’m pleased to announce steam locomotive 93 is back in service! The entire running gear underwent rebuilding. Locomotive 93 had been plagued with her axles running hot. For years, we have measured the axles’ temperature at Keystone; they always ran a little on the warm side. Then in July of 2007, the number two axle temperature shot up during an excursion. It was running so hot that we uncoupled the locomotive from the train at Lane City and had a diesel come out and bring the passenger train back in—very embarrassing.
Locomotive 93 stayed at Lane City and after the axle cooled, they limped back into town. The quick fixes that had worked in the past, wouldn’t work this time; the axle would not run cool. Locomotive 93 was rolled into the shop and axle 2 was dropped from the locomotive.
Now dropping a steam locomotive axle is no simple task. Luckily for us the machine shop and the engine house had a drop pit for lowering the axles. Over the past several years, we had rehabilitated the drop pit and the pit jack getting ready for the eventuality of needing to use it for dropping axles.
So we had the drop pit and the pit jack all set. The next trick was to remove all the rods from both sides of the locomotive. The rods transfer the power from the steam pistons to the wheels. The rods are on both sides of the locomotive. To remove a wheel set, the rods needed to come off. Again, we’re fortunate that we are able to do our repairs in the original railroad machine shop. The shop has the original overhead crane still in service. To take the rods off you run the overhead crane to where you’re working and lower the cable. A strap is wrapped around the rod. Then the very large nuts that hold the rods on are removed. The crane operator is signaled to raise the cable and slowly the slack is run out and the strap tightens and this is where the trick comes in. The workers on the ground need to have the crane just remove the weight from the pins that the rod sits on. If the cable goes up too high, the rods bind and can’t be removed. If the slack is too great, then when the rod is removed it could hit the ground or swing and injure one of the workers on the ground.
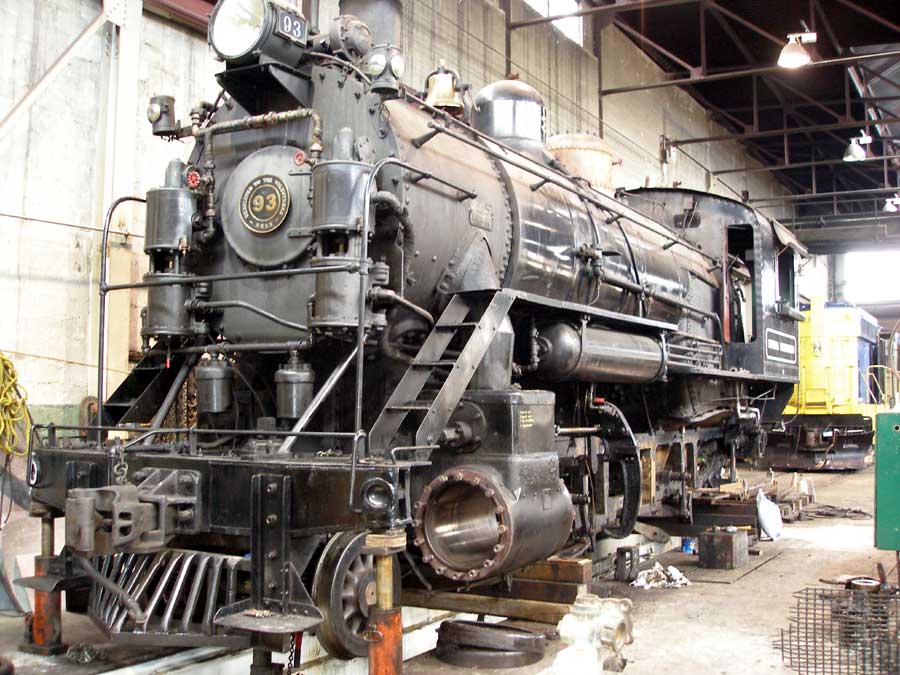
Locomotive 93 with all of the drivers and pistons removed.
What makes this even more interesting is it is obvious that when the crane was installed, labor was cheap. The crane operator rides in a basket with the crane. When the crane is in operation, the operator is in the basket. He or she is about thirty feet up in the air against the south wall of the shop. The locomotive is on the track against the north wall of the shop across from the crane operator. Doing the removal of the rods is like a ballet. The crane operator is closely watching the crew on the ground, waiting for hand signals, and listening for commands. The ground crew is positioning everything just so; at the right moment and at the right tension the nuts are removed and the rod is lifted off and placed on the floor out of the way.
Then the ballet continues. Now in the drop pit, the pit jack is moved into position under the axle. The frame binder is removed from under both sides of the axle. The jack is raised compressing the suspension springs. The rail under the wheel set is on a pivot and is swung out of the way. Now the wheel set is lowered below the locomotive frame. Now you need to move the wheel set out from under the locomotive. The pit jack is on wheels and the axle set is pushed out from under the locomotive. Remember labor being cheap when the machine shop was built? The wheel set is pushed out by brute strength. Once the wheel set is clear of the locomotive, the crane operator will lower the cable, lift the wheel set up out of the pit, and place it where the ground crew wants it. This is a heads-up operation. One false move and someone could be seriously injured; the wheel set weighs in at about 6,000 pounds.
This was in September 2007. Once axle 2 was on shop floor, it could be examined closely and it wasn’t a pretty picture. Still on the axles were the drive boxes, which contain the crown brasses. It was very evident that these were completely worn out.
Locomotive 93 is a 2-8-0 locomotive, meaning the locomotive has two pilot wheels and eight driving wheels. The locomotive weighs 187,000 pounds of which 168,000 pounds are on the drivers. So each driver is supporting 21,000 pounds or 10.5 tons.
The driver is on the track supporting the 10.5 tons. This weight is transferred through the tire to the wheel center and from the wheel center to the axle. From the axle, the weight is transferred to the crown brass. The crown brass is in the drive box and the drive box is in the frame with the shoes, wedges, and spring rigging. This combination supports the weight and it allows the locomotive wheel to move up and down as 93 goes down the track.
The key interface is the axle to the crown brass. This simple bearing rotates with a layer of grease separating the two parts through fluid dynamic effects. The axle and bearing are both simple polished cylinders with a lubricant filling the gap between them. Rather than the lubricant just “reducing friction” between the surfaces letting one slide more easily against the other, the lubricant is thick enough that once rotating the surfaces do not come in contact at all. Our problem was that the bearing surfaces on both the axle and the crown brass had imperfections that disrupted the fluid dynamics. Short version, the axle ran hot.
Our initial plan was to just repair axle number two. In December 2007, the axle was sent to a machine shop and put in a lathe to turn the bearing surface. Then another problem arose: in the process of turning the axle, cracks were discovered. All of them could be turned out except one. To turn out this crack would bring the axle down below its condemning limit. This was setback but it was also a wake-up call. It forced us to step-back from the locomotive and evaluate everything.
The axle was stamped 12-30-08 as in 1908. So after ninety-nine years, the axle was worn out and calls to the warranty department went unanswered. Discovering that crack started a chain reaction. First, it was decided to inspect ultrasonically all the axles. Axle 1 was from 1908, axle number 3 had been replaced in 1944, and axle 4 was replaced in 1927. What we found were axles 1 and 3 had cracks and axle 4 needed turning but was close to its condemning limit. In other words, all four axles needed to be replaced—this was a game changer.
Originally, our intention was just get 93 running again and out the door. But it was soon evident that if we were going to do the repairs that way, it would be a fool’s errand. Baling wire and bubble gum repairs simply will not sustain locomotive 93 over the long term.
Previous repairs had repaired the symptoms but did not tackle the reality that the locomotive was ninety-nine years old. In addition to the axles, the drive boxes, the crown brasses, the shoes, the wedges, the wheel centers, the tires, the crank pins, the spring rigging, the rod bearings, the cross heads, and the cross head guides all needed either refurbishment or replacement. Everything was worn out; in fact, rust was found on some of the bearing surfaces left there from when locomotive 93 spent thirty years outside in the elements.
The deeper we got into the locomotive the more that we found wrong. The first indication the project would be bigger than anticipated was when we removed the tires from the wheel centers. When the tires came off, it rained shims. This was unexpected. Once all of the tires were off, we had a little mountain of shims to deal with and a new unexpected problem—oversized tires.
Due to how closely all of the pieces of the running gear must work together, repairing one piece meant repairing another. For example, on the spring rigging the holes in the beams are suppose to be circular; they weren’t—they were oval. And the pins that held the beams in place looked liked like crankshafts rather than smooth rods.
The drive boxes were the biggest challenge and this is saying a lot because the entire process was a challenge. But the drive boxes are crucial to the entire system. They hold the crown brasses and axles and slide up and down in the locomotive frame. We welded them up and then machined new surfaces. Every surface that needed machining required what is called a set-up. We stopped counting the set-ups per box after we reached thirty-five (remember there are eight drive boxes). It might take hours to do a set-up and then just minutes to do the machining. To say this is labor intensive just doesn’t begin to explain it. There are eight individual boxes, but the machining needs to take into account how all of the boxes interface with the frame.
Our commitment to doing it right was expensive. We were taking care of problems there we left over from the 1940’s. Rebuilding a steam locomotive in the twenty-first century is a massive undertaking and not for the faint of heart. You just don’t go to Auto Zone for parts. Locomotive 93’s parts needed to be custom made, machined, fitted, checked, machined again, fitted, and checked. This is craftsmanship on a huge scale; the tolerances are unbelievably precise and the pieces are enormous.
But due to the combined efforts of the Heber Valley Railroad, Bonneville Machine Shop, Gary’s Machine Shop, and our staff and volunteers the running gear of locomotive 93 is better today than when she left her builder, the American Locomotive Company, a century ago.
On January 17, 2009 the Governor of the State of Nevada rededicated locomotive 93 at her 100th birthday party. “Engine 93, the fourth locomotive of the monster freight type ordered for ore line service…” and the remaining survivor is now ready for her second century of service.